What is Porosity in Welding: Crucial Tips for Getting Flawless Welds
What is Porosity in Welding: Crucial Tips for Getting Flawless Welds
Blog Article
Comprehending Porosity in Welding: Checking Out Reasons, Impacts, and Prevention Methods
Porosity in welding is a consistent challenge that can considerably influence the quality and stability of welds. As experts in the welding market are aware, understanding the reasons, effects, and avoidance techniques related to porosity is crucial for achieving robust and reliable welds. By diving right into the source of porosity, examining its harmful effects on weld high quality, and discovering efficient avoidance approaches, welders can improve their knowledge and skills to produce top quality welds regularly. The detailed interaction of factors adding to porosity needs a thorough understanding and a proactive technique to make sure effective welding end results.
Typical Reasons For Porosity
Contamination, in the type of dirt, oil, or corrosion on the welding surface, produces gas pockets when heated, leading to porosity in the weld. Incorrect securing happens when the securing gas, typically made use of in processes like MIG and TIG welding, is unable to fully shield the liquified weld swimming pool from reacting with the surrounding air, resulting in gas entrapment and succeeding porosity. Additionally, poor gas coverage, frequently due to wrong flow prices or nozzle positioning, can leave parts of the weld vulnerable, allowing porosity to create.
Effects on Weld High Quality
The existence of porosity in a weld can dramatically endanger the general quality and stability of the bonded joint. Porosity within a weld produces gaps or dental caries that weaken the structure, making it much more susceptible to splitting, corrosion, and mechanical failure.
Furthermore, porosity can impede the efficiency of non-destructive screening (NDT) methods, making it testing to spot other problems or gaps within the weld. This can cause considerable safety and security issues, particularly in crucial applications where the architectural integrity of the bonded parts is critical.

Avoidance Techniques Summary
Provided the destructive impact of porosity on weld top quality, reliable avoidance methods are essential to maintaining the structural integrity of welded joints. Additionally, selecting the appropriate welding parameters, such as voltage, current, and travel rate, can aid decrease the threat of porosity development. By integrating these prevention techniques into welding practices, the event of porosity can be significantly minimized, leading to more powerful and a lot more trusted bonded joints.
Significance of Proper Shielding
Correct securing in welding plays a vital duty in stopping atmospheric contamination and making certain the stability of welded joints. Securing gases, such as argon, helium, or a mix of both, are generally used to protect the weld swimming pool from reacting with elements airborne like oxygen and nitrogen. When these reactive components come into call with the hot weld swimming pool, they can trigger porosity, resulting in weak welds with decreased mechanical this contact form residential properties.
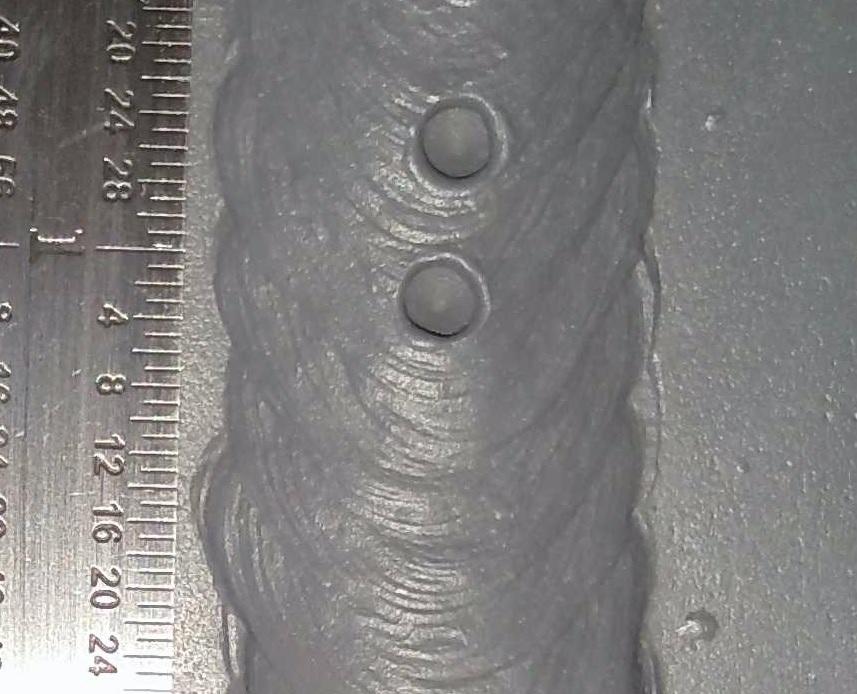
Insufficient protecting can cause various defects like porosity, spatter, and oxidation, jeopardizing the architectural stability of the welded joint. Adhering to proper shielding techniques is important to generate high-grade welds with very little defects and guarantee the long life and reliability of the welded components.
Monitoring and Control Approaches
Exactly how can look what i found welders successfully keep an eye on and manage the welding procedure to this ensure optimum outcomes and avoid defects like porosity? One key approach is through the use of advanced surveillance innovations. These can include real-time monitoring systems that give feedback on parameters such as voltage, existing, travel speed, and gas circulation prices. By continuously monitoring these variables, welders can recognize variances from the perfect conditions and make instant modifications to stop porosity formation.

Furthermore, executing correct training programs for welders is essential for keeping track of and controlling the welding process effectively. What is Porosity. Informing welders on the relevance of preserving regular criteria, such as proper gas securing and travel rate, can aid stop porosity concerns. Regular analyses and accreditations can additionally guarantee that welders are competent in monitoring and controlling welding processes
In addition, making use of automated welding systems can boost surveillance and control capabilities. These systems can precisely manage welding parameters, lowering the possibility of human mistake and guaranteeing constant weld high quality. By combining advanced tracking modern technologies, training programs, and automated systems, welders can properly monitor and regulate the welding procedure to reduce porosity issues and attain high-quality welds.
Verdict
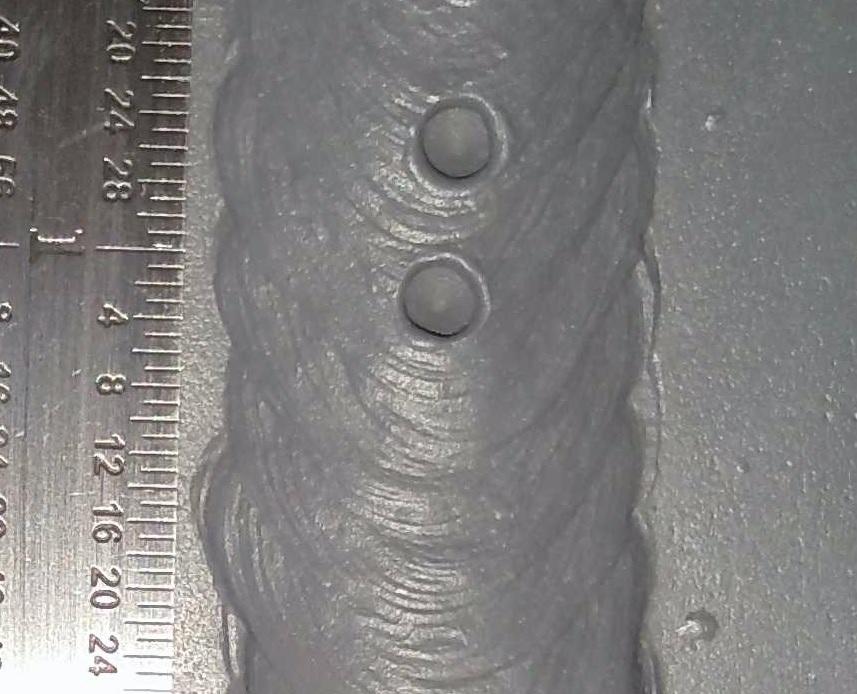
Report this page